Whether you’re building a dock, pier, or boathouse, a big part of your project will involve driving fasteners like framing nails, deck screws, and lag bolts. Make sure you choose hot-dipped galvanized fasteners that won’t rust, especially when exposed to water.
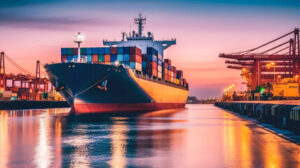
One popular trend in dock construction is building seating directly into the planking design. This eliminates the need for additional furniture, which can quickly wear and require replacement in a waterfront setting. Keep reading the article below to Learn More.
The location of a dock at the point where land meets water means that it has to be not only safe, but also extremely durable and strong. This means that constructing dock pilings from steel is an excellent choice. There are several different ways to do this, but blind bolts are a very popular option as they allow for a one-sided installation without having to disassemble the dock to access the fasteners. In addition, they provide a high level of safety by making it very difficult for unauthorized people to access the pilings and potentially cause damage or injury.
If you’re looking for the most strength and durability for your Muskoka dock, a steel-based pier is a great choice. Galvanized steel docks are known for their ability to withstand heavy usage and can stand up to the elements. They’re also less malleable than aluminum and are not as prone to corrosion, making them an ideal choice for a marine environment.
In terms of installation, a steel dock requires some specialized equipment. Coulsons uses a torque-driven steel pile system that drills each pile into the lakebed through the overburden (soil, sand and gravel). This method provides solid footings for your pier even in areas where there is no bedrock on the lake bottom. This is a major advantage for those whose docks may be subjected to the rigours of winter and the ice that forms on top of them.
This construction method allows you to enjoy your dock season after season, as the pier is very stable and can handle up to a four-foot change in water level. In addition, a steel-based pier can be used as a shoreline walkway and can easily support a wide variety of decking options. This gives you the opportunity to personalize your pier with your own unique style and create a waterfront experience that is both enjoyable and comfortable. If you’re ready to make your dream pier a reality, contact the experts at Rhino Dock today.
Concrete
Concrete docks are popular for their durability, longevity and resistance to corrosive marine elements. They can be designed to fit the needs of any project or budget, and are easy to install, maintain and repair. These structures are also ideal for areas with strong waves and winds that can damage pilings made of weaker materials. Depending on the mix of ingredients and installation method, concrete docks can withstand up to 50 years in harsh marine conditions.
Loading docks are exposed to heavy loads from vehicles and equipment that move in and out of the facility. They must be constructed to ensure safety for staff, and must comply with local building codes and regulations. This includes regulations for drainage/runoff provisions, and requirements for local frost lines that dictate the depth of the footings. It is also important to consider the logistics of the operation, since loading docks must be positioned to optimize freight traffic flow and to minimize potential hazards to drivers and other workers.
Choosing the right dock design for your facility depends on several factors, including the maximum expected trailer height and width, typical freight weights, and the amount of traffic to be accommodated over a given period. Generally, the best option is a fixed-height dock with a concrete pad. These docks are anchored to pilings that are drilled into the bed of the pond or lake, and a concrete deck is placed on top of them. The concrete is often reinforced with steel to help prevent cracks and to increase the load-bearing capacity.
In this study, a precast concrete structure known as the iDock was used to test GFRP as internal reinforcement in a marine application. The piles and pile caps were reinforced with GFRP bars from two dif- ferent manufacturers, whereas the slab recesses were reinforced with BFRP bars from a third manufacturer. Interaction diagrams and uplift loads were constructed to compare the performance of GFRP with conventional concrete for this application.
Foam is an inert material that doesn’t corrode, and it offers good protection against moisture and other environmental factors. It is typically sprayed with a mixture of fiberglass and cement, and it’s available in a variety of densities. The resulting coating is durable, lightweight and waterproof. It can be fabricated to fit the dimensions of any dock, and it allows utilities to be safely sealed within the core of the concrete dock section.
Polyethylene
Polyethylene (or PE) is a very common and versatile synthetic plastic. It is a member of the important family of polyolefin resins. Polyethylene has the chemical formula C2H4. It is an oily liquid at room temperature and it can be made into a variety of different shapes, sizes and products. It is one of the most widely used types of plastic, with applications ranging from food wrap and shopping bags to detergent bottles and automobile fuel tanks. Polyethylene is a stable, nontoxic and chemically resilient substance that resists biodegradation.
It is a thermoplastic, meaning that it can be melted and then cooled back into a solid many times without losing its shape. The properties of polyethylene depend strongly on the processing conditions. Different gauges of plastic can be produced, which can vary its impact strength, translucency, tensile/flexural strength and flexibility. The use of comonomers, crosslinking and additives can further modify the material’s characteristics.
Ethylene is a primary feedstock for the production of PE. It is a byproduct of petroleum hydrocarbon refinery processes and belongs to the naptha group of products along with propylene (C3H6), butene (C4H8), benzene and xylene. The polymerization of ethylene begins with the addition of an initiator to the liquid ethylene. A catalyst can also be added to help the process proceed. The most widely used catalysts for ethylene polymerization are the Phillips and Ziegler catalysts, which operate under mild temperatures and pressures.
The manufacturing of PE is accomplished through a combination of extrusion, injection molding and blow molding. It is very flexible, ductile and tough and can be formed into a wide variety of shapes. It can be melted into a sheet or film that is then stretched and extruded into the desired shape. It is also possible to make PE into a rod or tube.
Plastic docks are very affordable and easy to assemble. They are also environmentally friendly and require little maintenance. Wood docks require yearly painting and staining, and will eventually need to be replaced. With Connect-A-Dock, you can assemble your floating dock in less than five minutes per module.
Titanium
Titanium is an extremely durable, light-weight metal that’s often combined with other metals to create light-weight alloys for a variety of uses. It’s a great choice for marine applications because it’s resistant to corrosion from salt water and other marine environments. It also has good tensile strength and is not affected by oxidation in extreme conditions. In addition, titanium has a low thermal expansion coefficient and can be machined with ease.
Titanium’s ability to endure harsh marine environments makes it a natural choice for engineers to build ships from. It’s also highly biocompatible, which means it can be used in body parts such as hip replacements and dental implants. The material is also inert, which reduces the risk of it reacting with bodily fluids to cause inflammation.
In recent years, scientists and engineers have explored titanium’s ability to withstand aggressive oil refinery conditions. The material has shown that it can withstand high levels of chemical brines and brackish water. Its resistance to corrosive chemicals also makes it an ideal material for the construction of oil drilling platforms and pipelines.
A number of ship components and structures are now constructed from titanium because it’s lighter, stronger and longer lasting than steel. These include encapsulations for deep-diving submersibles, tensioner piston rods for the Snorre TLP and diving bell hatch doors, hydraulic cylinders for steering hydrofoil planes, jet foil inducers, process vessels and pumps, instrumentation, cable and pipe clamping systems and fasteners.
Although titanium is more expensive than steel on a pound-for-pound basis, it has a number of advantages over competing materials that make it a viable option for ship construction. It is weldable with conventional techniques and the strength of a titanium weld can exceed that of the parent metal. Its weldability and machinability help to lower the total cost of ownership of ship equipment.